How to Preserve Food with a Solar Dryer
Contents
Solar Drying - Technical Brief
Short Description
- Problem:
- Idea:
- Difficulty:
- Price Range:
- Material Needeed:
- Geographic Area:
- Competencies:
- How Many people?
- How Long does it take?
Introduction
Agricultural and other products have been dried by the sun and wind in the open air for thousands of years. The purpose is either to preserve them for later use, as is the case with food; or as an integral part of the production process, as with timber, tobacco and laundering. In industrialised regions and sectors, open air-drying has now been largely replaced by mechanised dryers, with boilers to heat incoming air, and fans to force it through at a high rate. Mechanised drying is faster than open-air drying, uses much less land and usually gives a better quality product. But the equipment is expensive and requires substantial quantities of fuel or electricity to operate.
'Solar drying' in the context of this technical brief, refers to methods of using the sun's energy for drying, but excludes open air 'sun drying'. The justification for solar dryers is that they may be more effective than sun drying, but have lower operating costs than mechanised dryers. A number of designs are proven technically and while none are yet in widespread use, there is still optimism about their potential.
How solar dryers work
One well-known type of solar dryer is shown in Figure 1. It was designed for the particular requirements of rice but the principles hold for other products and design types, since the basic need to remove water is the same.
Air is drawn through the dryer by natural convection. It is heated as it passes through the collector and then partially cooled as it picks up moisture from the rice. The rice is heated both by the air and directly by the sun.
Warm air can hold more moisture than cold air so the amount required depends on the temperature to which it is heated in the collector as well as the amount held (absolute humidity) when it entered the collector.
The way in which the moisture absorption capability of air is affected by its initial humidity and by the temperature to which it is subsequently heated is shown in Table 1.
Initial relative humidity |
Moisture absorption capability (grammes of water/m° of air) | ||
Not heated |
Heated to 40°C |
Heated to 60°C | |
40% |
4.3g/m° |
9.2g/m° |
16.3g/m° |
60% |
1.4g/m° |
8.2g/m° |
15.6g/m° |
80% |
7.1g/m° |
14.9g/m° |
Table 1: The drying process
The objective of most drying processes is to reduce the moisture content of the product to a specified value. Moisture content (wet basis) is expressed as the weight of water as a proportion of total weight. The moisture content of rice has typically to be reduced from 24% to 14%. So to dry one tonne of rice, 100kg of water must be removed.
If the heated air has a 'absorption capacity' of 8g/m3 then 100/0.0008 = 12,500/m3 of air are required to dry one tonne of rice.
The heat required to evaporate water is 2.26kJ/kg. Hence, approximately 250MJ (70kWh) of energy are required to vaporise the 100kg water. There is no fixed requirement for solar heat input to the dryer. This is because the incoming ambient air can give up some of its internal energy to vaporise the water (becoming colder in the process). Indeed, if the ambient air is dry enough, no heat input is essential.
Nevertheless, extra heat is useful for two reasons. First, if the air is warmer then less of it is needed. Second, the temperature in the rice grains themselves may be an important factor, especially in the later stages of drying, when moisture has to be 'drawn' from the centres of the grains to their surfaces. This temperature will itself depend mainly on the air temperature but also on the amount of solar radiation received directly by the rice.
In a natural convection system, the flow of air is caused by the fact that the warm air inside the dryer is lighter than the cooler air outside. This difference in density creates a small pressure difference across the bed of grain, which forces the air through it. This effect increases, the greater is the height of the bed above the inlet (h1) and the outlet above the bed (h2). The effect of an increased h2 is less than that of an increased h1 because the air is cooled as it passes through the bed.
Approximate densities for a variety of cases are shown in Table 2.
Initial relative humidity |
Density of the air (kg/m3) (Drop in density, in brackets) | |||
Not heated |
Heated to | |||
30 °C |
40 °C |
60 °C | ||
40% |
Ambient 1.19 |
1.19 |
1.19 |
1.19 |
Below bed 1.19 (.00) |
1.15 (.04) |
1.12 (.07) |
1.05 (.14) | |
Above bed 1.21 (-.02) |
1.19 (.00) |
1.17 (.02) |
1.14 (.05) | |
60% |
Ambient 1.19 |
1.19 |
1.19 |
1.19 |
Below bed 1.19 (.00) |
1.15 (.04) |
1.11 (.08) |
1.05 (.14) | |
Above bed 1.20 (-.01) |
1.18 (.01) |
1.16 (.03) |
1.13 (.06) | |
80% |
Ambient 1.18 |
1.18 |
1.18 |
1.18 |
Below bed 1.18 (.00) |
1.14 (.04) |
1.11 (.07) |
1.04 (.14) | |
Above bed 1.18 (.00) |
1.16 (.02) |
1.15 (.03) |
1.11 (.07) |
Table 2: Air density variation in a natural convection dryer
It can be seen that if the incoming air is heated by only 10-30°C then the presence of a chimney on top of the dryer would make little or no difference, unless it acted efficiently as a solar collector and raised the temperature of the air significantly.
It should be noted that even if the difference in densities is as much as .05kg/m2, then the resulting pressure difference is only 0.5 Pa (5 millionths of atmospheric pressure) per metre of chimney. For comparison, forced convection systems commonly operate with pressure differences of 100-500 Pa.
Many products are damaged by excessive temperatures. The most severe constraints are on beans (35°C), rice (45°C), and all grains if they are to be used for seed (45°C).
Other types of dryers and their performance
Forced convection solar dryer
(Figure 2)
By using a fan to create the airflow, drying time can be reduced by a factor of 3. Also, the area of collector required is reduced by up to 50%. Therefore, the area of collector required for a given throughput of product could be reduced by a factor of 5-6. The initial cost of a one tonne per day dryer is in the region of £1500-2000. The fan would consume about 500 watts for 6 hours, and so electricity cost (at 0.07/kWhr) would be about 0.20 per tonne of rice dried
Tent dryer
The distinguishing feature of tent, box and cabinet dryers is that the drying chamber and the collector are combined into one, see Figure 3. This allows a lower initial cost. Drying times are however not always much lower than for open-air drying. (Probably, insufficient attention has so far been paid to utilising natural convection.) The main purpose of the dryers may be to provide protection from dust, dirt, rain, wind or predators and they are usually used for fruit, fish, coffee or other products for which wastage is otherwise high. There are numerous other types. Greenhouse dryers are a more sophisticated version of tent dryers. Box dryers may incorporate thermal insulation to achieve higher temperatures. Storage bin dryers combine the functions of drying and long-term storage. Solar timber kilns may include hot water storage to enable the necessary control of drying rate.
Solar drying or open-air drying?
The great advantage of open-air drying is that it has little or no equipment costs. It is labour-intensive but this may not involve much economic cost in rural areas in developing countries. It requires about three times as much land (100m2 per tonne of rice) compared to solar drying, but this may not matter too much in many cases.
Firstly, one important advantage of solar drying is that the product is protected from rain, insects, animals and dust that may contain faecal material. Some systems also give protection from direct sunlight. Second, faster drying reduces the likelihood of mould growth. Third, higher drying temperatures mean that more complete drying is possible, and this may allow much longer storage times (but only if rehumidification is prevented in storage). Finally, more complex types of solar dryers allow some control over drying rates.
Solar dryers or fuelled dryers?
The choice between using solar radiation or fuel, to heat the air is mainly one between a higher initial cost and continuing fuel costs which needs to be analysed for each location.
In some circumstances, it may be possible to burn rice husks or other fuel with low opportunity cost. One tonne of rice gives 200kg of husks.
Fuel heating usually allows better control of the drying-rate than solar heating; it also enables drying to be continuous. If either of these is required, a combined system may be appropriate with pre-heating of air by solar energy.
Which solar dryer?
The choice between alternative types of solar dryer will depend on local requirements and in particular on the scale of operation. If intended for peasant farmers then initial capital cost may be the main constraint and plastic-covered tent or box dryers may be appropriate.
There may however be a trend towards more centralised drying to enable more intensive usage of the equipment. The greater initial cost of glass covers may then be affordable, and grid electricity may be available to run fans and obtain much faster throughput for a given collector area.
For intermediate scale and capital cost the natural convection rice dryer is a well proven design.
References and further reading
This Howtopedia entry was derived from the Practical Action Technical Brief Solar Drying.
To look at the original document follow this link:
http://www.practicalaction.org/?id=technical_briefs_food_processing
A survey of solar agricultural driers - Brace Research Institute - 1975
Preparing grain for storage - Action/Peace Corps and VITA - 1976
Solar driers - Commonwealth Science Council - 1985
Solar drying - Practical methods of food preservation - ILO 1988
Producing Solar Dried Fruit and Vegetables for Small-scale Enterprise Development - NRI 1996
Try Drying It!: Case studies in the dissemination of tray drying technology - IT Publishing 1991
Related Articles
- How to Preserve Food with Small Scale Drying Technologies
- How to Preserve Food by Drying
- How to Use Sun Power
- How to Make Chocolate
- How to Preserve Tomato
- How to Preserve Food with a Solar Dryer
- How to Process Spice
- How to Process Turmeric
- How to Build a Tray Dryer
- The Anagi Tray Dryer
- How to Dry Chillies
- How to Process Pepper
Useful addresses
Practical Action
The Schumacher Centre for Technology & Development, Bourton on Dunsmore, RUGBY, CV23 9QZ, United Kingdom.
Tel.: +44 (0) 1926 634400, Fax: +44 (0) 1926 634401
Email: practicalaction@practicalaction.org.uk web:http://www.practicalaction.org
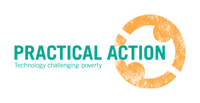
NR International
Central Avenue Chatham Maritime, Kent, ME4 4TB, United Kingdom
Tel: +44 1634 880088, Fax: +44 1634 880066/77
Website: http://www.nrinternational.co.uk/