How to Measure the Energy Used to Fire Clay Bricks
How to Measure the Energy Used to Fire Clay Bricks -
A Practical Guide for Brickmakers, Field-Workers and Researchers - Technical Brief
Introduction
In 1996 Practical Action (then ITDG) undertook a project working with small-scale brickmakers in Peru, Ecuador and Zimbabwe. The idea is to disseminate appropriate, energy efficient principles and practices. But what is an energy efficient brick firing technology? How do you measure it? And how do you compare it with technologies used in other places?
Data on energy use in brickmaking has generally been collected and presented in a random fashion. It's often of very little use when trying to evaluate and compare processes. For example, a report may state 'brickmakers use four sacks of coal to fire a thousand bricks.' Fine, but what does this tell us about the energy used? We don't know the mass of a sack of coal. We don't know its calorific value. And we don't know anything about the bricks. What type of soil are they made from, and how much heat is needed for vitrification - the formation of the ceramic bond? How wet were they going to the kiln - how much fuel was used simply to dry them? What is their mass? (Bigger, heavier bricks obviously take more energy to fire.) And how well burned are they? In short, we know next to nothing useful.
This technical brief details a way of gathering and presenting information on brick firing. If the method is followed, it will allow not only the energy use of a particular kiln to be calculated, but also the efficiency to be compared to others world-wide. There are difficulties involved in establishing a methodology. For example, some scientific knowledge is implicit. Also, facilities around the world and the resources available to those monitoring brick firing will be different. As far as possible, the method presented here minimises costs and the need for specialist services.
Figure 1: Brickmaker lighting kiln with liquid fuel . ©Practical Action
Figure 2:Firing bricks using firewood as a fuel . ©Practical Action
Background
The factors which affect energy use in brickmaking are:
• The nature of the clay: refractoriness - resistance to change by heat; the presence of fluxes - substances which aid vitrification; intrinsic calorific value.
• The moisture content of 'green' bricks going into the kiln.
• The type of fuel used, its calorific value, moisture content, and distribution.
• The design of kiln.
• The skill of the brickmakers controlling the burning process
• The climatic conditions: ambient temperature, wind direction and strength...
Normally, it's the effect of kiln design which is being investigated. Either that or varying the operating conditions of similar kilns. Here, the way we gather data takes account of the nature of the clay and its effect on energy consumption. We also consider only the energy used in firing, ruling out drying energy, so we can compare processes directly. Then we propose a way of measuring how much heat-work has actually been done - this is so we can take account of how well bricks are fired. (It would be easy to think a process was efficient because it used very little energy and then find the bricks were only dried mud - not vitrified at all!)
Data collection
We categorise clay as high temperature (vitrifying above 1,000°C), medium temperature (vitrifying between 950 and 1,000°C), or low temperature (vitrifying below 950°C). This means access to a laboratory kiln which can reach such temperatures. The procedure is to mould cones approximately 70 mm high with a base diameter around 15 mm. Cones are placed in the kiln leaning slightly so that when vitrification temperature is reached the top bends over. This temperature is noted and the clay categorised accordingly.
The exact number of bricks being fired is needed. This is easier to determine if bricks are stacked in thousands prior to firing. Alternatively, the bricks in each layer can be counted as the kiln is built. Then we need to know the mass of the bricks. A convenient number of green bricks (perhaps 1 per 1,000, but not less than 24) should be selected at random and weighed. Thence an average 'wet mass' can be calculated. Now we need to know the moisture content of the green bricks to calculate the energy needed simply to dry them. The selected bricks can be dried in a conventional oven or a simple field oven. The important thing is to keep bricks between 80 and 100°C and weigh them periodically until no further weight loss is noted. The average 'dry mass' can then be found. With this data it's possible to calculate the mass of water and the drying energy:
Mass of green bricks = avg. mass of green brick x no. of bricks
Total moisture content = moisture content of brick x mass of bricks
Drying energy = specific drying energy x total moisture content
(Where specific drying energy' = 2,591 kJ/kg of moisture)
All fuel used should be weighed. If a fuel such as saw-dust or pulverised fly ash is mixed into the body of bricks, its mass must also be determined. A sample of each fuel used should be taken promptly to test for calorific value and moisture content. If the clay has a natural fuel content, it too should be sent for testing.
If such test facilities are unavailable or unaffordable, then the best that can be done is to use the most recent local data. If a value is found in this way, it should not be recorded as the specific calorific value and a note should be made of the source of the information. From this data the total energy used is calculated:
Total energy = mass of fuel x net calorific value
And the firing energy is obtained by subtracting the energy used for drying
Firing energy = total energy - drying energy
We need to know how well bricks are fired, or rather the heat-work done. Testing brick properties such as compressive strength will not give useful data to compare kilns because properties are affected by factors other than firing. The effectiveness of a firing process is a function of time and temperature, but the relationship is not linear. Bricks fired at 1,000°C for 10 hours would not be the same as bricks fired at 100°C for 100 hours! We could plot temperature against time for various points in the kiln and present this graphically to qualify energy use. However, thermometry to measure such high temperatures is expensive1.
1 At 1998 prices, thermometry to monitor a 20,000 brick kiln would cost approximately £1,500 (obviously this hardware should be re-usable). Using Bullers Bars would cost about £70 per kiln.
A more affordable alternative is to use Bullers Bars2 placed strategically in the kiln. Bullers Bars are about 57 mm long and are made from ceramic material which melts at set temperatures. They come in a range from 590 to 1,525°C. Four bars which melt at different temperatures can be placed on a refractory stand to form a 'thermoscope'. Thermoscopes are placed as required in the kiln.
2 Bullers Bars can be obtained from Taylor Tunnicliff Ltd., Normacot Road, Longton, Stoke-on-Trent, ST3 1PA, UK; tel. 44 (0)1782 501174; fax. 44 (0)1782 328807; </u>; Internet, http://www.taylortunnicliff.co.uk/products.htm
Once the kiln is fired and cooled, a representative sample of bricks - the same number as before - should be weighed, and the average fired mass calculated. Now we can calculate the total mass of fired brick and the specific firing energy:
Mass of fired brick = mass of a fired brick x number of fired bricks
Presenting results
Ultimately, the results of a brick firing process would consist of:
• The specific energy used.
• The moulding process.
• The clay vitrification temperature categorisation.
• The Buller's Bar numbers for different locations, and/or an average number.
• A statement of qualifying information, comments and observations
This brief contains a photocopiable monitoring form for recording data and calculations. There is also an example of a completed form for guidance, and a checklist to ensure all the vital data has been recorded.
Checklist
The following is a list of information which must be noted:
Monitoring form: Energy consumption of brick firing processes
Name of producer Fambidzanai Training Centre (FTC) |
Location/address 4 Dovedale Rd, Stapleford, Mount Hampden, Harare. |
Dates and times of firing Start 1 Jan. 1998 |
Type of clamp/kiln Layered, scoved clamp |
Type of fuel Boiler waste |
Mass of fuel used (kg) 4,680 |
Calorific value (kJ/kg) Gross 20,170 |
No. of green bricks in kiln 14,817 |
Mass per brick (kg) green 3.65 |
Brick moisture content (%) = (3.65 - 3.25) x 100/3.65 |
Method of forming Semi-dry pressing (Ceratec press machine) |
Weather conditions Intermittent heavy rain, but clamp sheltered by roof |
Calculation of kiln efficiency Mass of green brick (kg) 14,817 x 3.65 = 54,082 |
Qualifying information: (i) Soil vitrification category And/or (iii) Avg. firing temp. (°C)? | |
Notes: ‡Thermoscopes contained bars 11, 13, 15 & 17. Only six of eighteen were recovered. Three from the sides of layers 4 and 15 and the centre of layer 26 were virtually unaffected. One from the side of layer 8 showed Bar no. 13 just sagging. Two, from layer 14 (centre) and layer 18 (side) had all the bars melted - turned totally to liquid in layer 14. With only six samples it's not really valid to take an average. Comments: Bricks are mostly underfired. Specific firing energy is thus quite low. The long firing time indicates not enough air gaps - boiler waste packs 'tighter' than coal. Brick quality and appearance is not good due to poor soil preparation, a worn press machine, and contamination from to drying on dirty ground. Bricks are easily broken, revealing no unfired core, but a matrix containing lumps of dry clay and stones - stones too big to make a strong brick. Bricks aren't vitrified but merely quite well 'baked'. Some were 'hard-burned' - turning blue. These corresponded to 'hot-spots' indicated by Thermoscopes. Clamp volume is 39 cubic metres while the volume of bricks is around 27 cubic metres. Void volume is thus 12 cubic metres (about 30%) which includes the volume of coal initially in the clamp. Recommendations: Green bricks should be thoroughly dry to save fuel. The firing process needs modifying to produce well burned bricks. The 'high temperature' soil is difficult to vitrify, needing a temperature of more than 1000°C. Experience suggests fuel should be increased by around 20%. More sensibly, this increase could be achieved by ensuring green bricks are dry. The same fuel to brick mass ratio could then be retried. The other problem is air flow. The clamp burned too slowly. Boiler waste could be distributed more evenly throughout, and air gaps between bricks could be increased. Firing time could be reduced to around 7 days. Signature, date, organisation & contact address |
Name of producer |
Location/address |
Dates and times of firing Start |
Type of clamp/kiln |
Type of fuel |
Mass of fuel used (kg) |
Calorific value (kJ/kg) Gross |
No. of green bricks in kiln |
Mass per brick (kg) |
Brick moisture content (%) |
Method of forming |
Weather conditions |
Calculation of kiln efficiency Mass of green brick (kg) |
Qualifying information: (i) Soil vitrification category And/or (iii) Avg. firing temp. (°C) | |
Comments Signature, date, organisation & contact address |
Equipment Suppliers
TARA Machines & Tech Services Pvt. Ltd.
29, Ghitorni, Mehrauli–Gurgaon Road
New Delhi – 110030
Tele-fax - +91–11– 26801521, 26804482, 26805826
Website: www.taramachines.com
- Energy efficient brick firing Klin TARA Eco Kiln
- High quality brick moulding TARA Brickmek Moulding
References and further reading
• Ten Rules for Energy Efficient, cost Effective Brick Firing: A Guide for Brickmakers and Field-workers Practical Action Technical Brief
• Sustainable Small Scale Brick Production: A question of energy, Theo Schilderman, 1999, Practical Action Technical Brief
• Assessing the Technical Problems of Brick Production a Guide for Brickmakers and Field-Workers, Practical Action Technical Brief
• Evolving a Standard to Compare the Energy Efficiency of Brick Firing Processes, Kelvin Mason & Ray Austin, Practical Action Technical Brief, 1998
• Drying of Clay Bricks and Tiles GATE Technical Brief, Gerhard Merschmeyer, 1999,
http://www2.gtz.de/Basin/gate/tb12/claydrying.zip
• Moulding of Clay GATE Technical Brief, Gerhard Merschmeyer, 2001,
http://www2.gtz.de/Basin/gate/tb15/ClayMoulding.ZIP
• Brick Clamps GATE Technical Brief, Tim Jones, 1995,
http://www2.gtz.de/Basin/gate/brickclamps.htm
• Bull's Trench Brick Kiln GATE Technical Brief, Henrik Norske, 1995,
http://www2.gtz.de/Basin/gate/bull.htm
• Hoffmann Kilns GATE Technical Brief, Tim Jones, 1995,
http://www2.gtz.de/Basin/gate/HoffmannKilns.htm
• The Vertical Shaft Brick Kiln GATE Technical Brief, Tim Jones, 1997,
http://www2.gtz.de/Basin/gate/vertical.htm
• Firing of Clay Bricks & Tiles, GATE Technical Brief, Gerhard Merschmeyer, 2000,
http://www2.gtz.de/Basin/gate/tb13/clayfiring.zip
• Village Level Brickmaking, Anne Beamish & Will Donovan, GATE/Friedr. Vieweg & Sohn, Braunschweig, Wiesbaden, 1989, http://www2.gtz.de/Basin/publications/books/village.pdf
• The Clay Industry: Improvement of Resource Efficiency and Environmental Performance, CleanerProduction.Com, http://www.cleanerproduction.com/sectors/subsectors/clay.html
• How to Start a Small Clay Brick and Tile Making Enterprise, GATE/GTZ Question & Answer, Responses to Frequently Asked Questions,
http://www2.gtz.de/Basin/knowledgebase/search/showrecord.asp?D=4&P=436&A=1
• What Type of Kiln Should Be Chosen for Firing Clay Brick and Roofing Tiles, GATE/GTZ Question & Answer, Responses to Frequently Asked Questions,
http://www2.gtz.de/Basin/knowledgebase/search/showrecord.asp?D=4&P=446&A=1
This Howtopedia entry was derived from the Practical Action Technical Brief ‚Assessing the Technical Problems of Brick Production a Guide for Brickmakers and Field-Workers.
To look at the original document follow this link: http://www.practicalaction.org/?id=technical_briefs_energy
Back cover
This technical brief was originally written for basin, Building Advisory Service and Information Network by Kelvin Mason, April 1998 on behalf of ITDG. Special thanks to Ray Austin, Dr Alfredo Barriga (ESPOL) and Mario Jara. Website: http://www.gtz.de/basin For further information contact: Practical Action Practical Action Latin America This Technical Brief was possible thanks to the collaboration of DFID-UK and The Tony Bullard Trust |
Useful addresses
Practical Action
The Schumacher Centre for Technology & Development, Bourton on Dunsmore, RUGBY, CV23 9QZ, United Kingdom.
Tel.: +44 (0) 1926 634400, Fax: +44 (0) 1926 634401
e-mail:practicalaction@practicalaction.org.uk
web:www.practicalaction.org
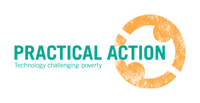
Categories
- Medium
- Between 2 and 5 People
- Principles
- Global Technology
- Energy
- Construction
- Ideas
- Products
- Recycling
- Small Business
- Waste
- Dangerous
- Difficult
- High Technology
- Monsoon Climate
- Montaneous Environment
- Rural Environment
- Temperate Climate
- Tropical Climate
- Urban Environment
- Ashes
- Coal
- Clay
- Rice Husk
- Bricks
- Howtopedia requested drawings
- Howtopedia requested images
- Requested translation to Spanish
- Requested translation to French