Biomasse et biocarburants liquides
Sommaire
Description brève
- Type d'information: principes
Introduction
Contexte
Biomass residues can also be converted into various non-solid fuel forms. These fuels are referred to as biogas and liquid biofuels. The aim of this conversion process is to improve the quality, specific energy content, transportability, etc., of the raw biomass source or to capture gases which are naturally produced as biomass is micro biologically degraded or when biomass is partially combusted. Biogas is a well-established fuel for cooking and lighting in a number of countries, whilst a major motivating factor in the development of liquid biofuels has been the drive to replace petroleum fuels. In this fact sheet we will be looking at some of these fuels, their applications and the conversion technologies used to derive them.
In Europe and the United States, as well as in several developing countries, there is a move toward cultivating energy crops specifically for the production of biomass as a fuel. The potential for energy production from biomass throughout the world is enormous and as fossil-based fuels become scarcer and more expensive, as carbon emission levels are becoming of greater concern and as people realise the benefits of developing integrated energy supply options, then biomass could begin to realise its full potential as an energy source.
Technical
Biogas
Biogas is produced by means of a process known as anaerobic digestion. It is a process whereby organic matter is broken down by microbiological activity and, as the name suggests, it is a process which takes place in the absence of air. It is a phenomenon that occurs naturally at the bottom of ponds and marshes and gives rise to marsh gas or methane, which is a combustible gas.
There are two common man-made technologies for obtaining biogas, the first (which is more widespread) is the fermentation of human and/or animal waste in specially designed digesters. The second is a more recently developed technology for capturing methane from municipal waste landfill sites. The scale of simple biogas plants can vary from a small household system to large commercial plants of several thousand cubic metres.
The digestion of animal and human waste yields several benefits:
- the production of methane for use as a fuel. The waste is reduced to slurry which has a high nutrient content which makes an ideal fertiliser; in some cases this fertiliser is the main product from the digester and the biogas is merely a by-product. During the digestion process bacteria in the manure are killed, which is a great benefit to environmental health.
Two popular simple designs of digester have been developed; the Chinese fixed dome digester and the Indian floating cover biogas digester (shown in figures 1& 2). The digestion process is the same in both digesters but the gas collection method is different in each. In the floating cover type, the water sealed cover of the digester is capable of rising as gas is produced and acting as a storage chamber, whereas the fixed dome type has a lower gas storage capacity and requires good sealing if gas leakage is to be prevented. Both have been designed for use with animal waste or dung.
The waste is fed into the digester via the inlet pipe and undergoes digestion in the digestion chamber. The temperature of the process is quite critical - methane producing bacteria operate most efficiently at temperatures between 30 - 40°C or 50 - 60°C and in colder climates heat may have to be added to the chamber to encourage the bacteria to carry out their function. The product is a combination of methane and carbon dioxide, typically in the ratio of 6:4. Digestion time ranges from a couple of weeks to a couple of months depending on the feedstock and the digestion temperature. The residual slurry is removed at the outlet and can be used as a fertiliser.
Biogas has a variety of applications. Table 1, below, shows some typical applications and for one cubic metre of biogas.
Small-scale biogas digesters usually provide fuel for domestic lighting and cooking.
Application |
1m3 biogas equivalent |
Lighting |
equal to 60 -100 watt bulb for 6 hours |
Cooking |
can cook 3 meals for a family of 5 - 6 |
Fuel replacement |
0.7 kg of petrol |
Shaft power |
can run a one horse power motor for 2 hours |
Electricity generation |
can generate 1.25 kilowatt hours of electricity |
Table 1: some biogas equivalents
Source: adapted from Kristoferson, 1991.
Some countries have initiated large-scale biogas programmes, Tanzania being an example. The Tanzanian model is based on integrated resource recovery from municipal and industrial waste for grid-based electricity and fertiliser production.
Biomass gasification
The process of biomass gasification is distinctly different form that of biogas production. Gasification is the process by which solid biomass materials are broken down using heat to produce a combustible gas, commonly known as producer gas. Common feedstocks for combustion include wood, charcoal, rice husks and coconut shells.
The biomass gasification plant consists of a reactor, similar to a simple stove, into which the solid biomass fuel is fed. The supply of air to the fuel is, however, carefully controlled to allow only partial combustion of the fuel to take place. During this process gases are given off which are captured and can be used as a fuel gas. Several combustible gases are given off - hydrogen, carbon monoxide and methane - as well as carbon dioxide and nitrogen.
Two reactor types exist; the fluidised bed reactor, which is used with large-scale gasification system, and the fixed bed reactor, which is employed for small-scale producer gas systems. There are three varieties of fixed bed reactor; updraft, downdraft and crossdraft. Each reactor type produces a different ratio of gases at different temperatures and with a differing level of cleanliness.
The gas has several applications. It can be used directly in a burner to provide process heat or it can be used in internal combustion engines, but requires cleaning and cooling for this application. Plant ratings for small-scale power output can range from several kilowatts up to several hundred kilowatts and for heat production the output can be several megawatts. System efficiencies vary considerably depending on fuel, reactor type and application. Producer gas is commonly used for commercial cooking applications.
The small-scale gasifier technology is reasonably simple and cheap and can be manufactured locally, although care should be taken to ensure safety standards are maintained as carbon monoxide, which is produced during combustion, is a toxic gas. In China, a downdraft reactor design has been in production since the 1960's which uses rice husks as feedstock and hundreds of these systems are in use. They have also been installed in Mali, Surinam and India (Stassen 1995). During the Second World War, when fuel supplies were in short supply, millions of vehicles in Europe were adapted to run on producer gas, and today in countries such as Brazil and the Philippines gasifiers are commercially available for a variety of applications.
Liquid biofuels
Liquid biofuels, as their name suggests, are fuels derived from biomass and processed to produce a combustible liquid fuel. There are two main categories:
alcohol fuels - these include ethanol and methanol vegetable oils - derived from plant seeds, such as sunflower, sesame, linseed and oilseed rape.
Ethanol is the most widely used liquid biofuel. It is an alcohol and is fermented from sugars, starches or from cellulosic biomass. Most commercial production of ethanol is from sugar cane or sugar beet, as starches and cellulosic biomass usually require expensive pretreatment. It is used as a renewable energy fuel source as well as being used for manufacture of cosmetics, pharmaceuticals and also for the production of alcoholic beverages.
The substitution of ethanol for gasoline in passenger cars and light vehicles in Brazil is one of the largest biomass-to-energy programmes in existence today. Engines that run strictly on gasoline are no longer available in the country, having been replaced by neatethanol engines and by gasohol engines that burn a mixture of 78 per cent gasoline and 22 per cent ethanol by volume.Technological advances, including more efficient production and processing of sugarcane, are responsible for the availability and low price of ethanol. The transition to ethanol fuel has reduced Brazil's dependence on foreign oil (thus lowering its importexport ratio), created significant employment opportunities and greatly enhanced urban air quality. In addition, because sugarcane-derived ethanol is a renewable resource (the cane is replanted at the same rate it is harvested), the combustion of ethanol adds virtually no net carbon dioxide to the atmosphere and so helps reduce the threat of global warming. |
Source: Goldemberg et al, Renewable Energy, Sources for Fuels and Electricity, 1993
Methanol is produced by a process of chemical conversion. It can be produced from any biomass with a moisture content of less than 60%; potential feedstocks include forest and agricultural residues, wood and various energy crops. As with ethanol it can either be blended with gasoline to improve the octane rating of the fuel or used in its neat form. Both ethanol and methanol are often preferred fuels for racing cars.
Vegetable oils
A further method of extracting energy from biomass is the production of vegetable oils as a fuel known as biodiesel. The process of oil extraction is carried out the same way as for extraction of edible oil from plants. There are many crops grown in rural areas of the developing world which are suitable for oil production - sunflower, coconut, cotton seed, palm, rapeseed, soy bean, peanut, hemp and more. Sunflower oil, for example, has an energy content about 85% that of diesel fuel.
There are two well-established technologies for oil extraction:
The simple screw press, which is a device for physically extracting the oil from the plant - this technology is well suited to small-scale production of oil as fuel or as foodstuff in rural areas. The press can be motorised or hand-operated. Solvent extraction is a chemical process which requires large, sophisticated equipment. This method is more efficient - that is, it extracts a greater percentage of the oil from the plant - but is less suited to rural applications.
The oil, as well as being used for lighting and heating, can be used as a fuel in internal combustion engines.
Biodiesel production is not complex and can be done on a small scale. The vegetable oil is converted to a useable fuel by adding ethanol or methanol alcohol along with a catalyst to improve the reaction. Small amounts of potassium hydroxide or sodium hydroxide (commonly called lye or caustic soda, which is used in soapmaking) are used as the catalyst material. Glycerine separates out as the reaction takes place and sinks to the bottom of the container. This removes the component that gums up the engine so that a standard diesel engine can be used. The glycerine can be used as a degreasing soap or refined to make other products.
Other issues
Present status
Small-scale biogas production in rural areas is now a well-established technology, particularly in countries such as China and India. At the end of 1993, about five and a quarter million farmer households had biogas digesters, with an annual production of approximately 1.2 billion cubic metres of methane, as well as 3500 kW installed capacity of biogas fuelled electricity plant.
In India, there has been widespread development and dissemination of gasification technology to meet a variety of rural energy needs - for example, irrigation pumping and village electrification.
Ethanol production programmes have been initiated in several developing countries. The success of the Brazilian programme is mentioned earlier in this technical brief while in Zimbabwe for example, an annual production of about 40 million litres has been possible since 1983, using locally manufactured equipment.
Biomass energy and the environment
There are two areas of environmental concern when considering using biomass as a form of energy. Firstly, there is the issue of land degradation and deforestation. This concern can be addressed by proper management of sustainable energy crops. Although much of the biomass requirement for energy production can be met through utilising residues from the food industry, from agriculture or from commercial activity, careful planning of energy cropping is required to prevent undue stress on the environment.
With the recent global call to reduce carbon dioxide emissions, there is a strong case for promoting the use of sustainable biomass-to-energy technologies worldwide. Using modern technology, enormous reductions can be made in carbon dioxide emissions, particularly if liquid biofuels are used to replace their fossil-based equivalents. In fact, if biomass energy production is done on a sustainable basis, there is little net carbon dioxide addition to the environment.
There are other environmental concerns related to each fuel that need to be kept in mind, such as toxic emissions and production of tars and soots.
Local manufacture and involvement
Many biomass conversion technologies for rural applications are easily manufactured by local artisans or by small and medium sized engineering workshops. In Zimbabwe, locally made equipment for large scale ethanol production has led to the lowest capital cost per litre for any ethanol plant in the world.
In China and India biogas plants are produced in great numbers by local artisans. In Kenya, where biogas technology is still in its early stages of dissemination, local manufacturers have been quick to realise the potential and get involved with the production of biogas plants.
Dissemination
Kenya relies on imported petroleum to meet 75% of its commercial energy needs. In 1980, in an effort to reduce this high level of dependence on an externally controlled fuel source, the Kenyan government set up the Special Energy Programme (SEP). One aspect of the programme was the introduction and dissemination of biogas plant technology. After a poor start working with educational institutions, the programme turned to local artisans and commercial outlets working in the private sector. Hands-on training was given to masons and plumbers and private traders were encouraged to manufacture and stock appliances such as cookers and lights. By 1995, the number of plants installed in Kenya was estimated to be 880.
References and resources
Ravindranath, N. H. and Hall, D. O., Biomass, Energy and the Environment: A Developing Country Perspective from India. Oxford University Press, 1995.
Karekezi, S. and Ranja, T., Renewable Energy Technologies in Africa. AFREPEN, 1997.
Kristoferson L. A., and Bokalders V., Renewable Energy Technologies - their application in developing countries. ITDG Publishing, 1991.
Johansen, T.B. et al, Renewable Energy Sources for Fuels and Electricity. Island Press, Washington D.C., 1993.
Gunnerson C. G. and Stuckey D. C., Anaerobic Digestion - Principles and Practices for Biogas Systems. World Bank Technical Paper No 49, The World Bank, 1986.
Gitonga, Stephen, Biogas Promotion in Kenya. Intermediate Technology Kenya, 1997.
Stassen, H.E., Small-scale biomass gasifiers for heat and power: a global review. World Bank technical paper no. 296, Energy Series 1995.
Quaak, P., Knoef, H. and Stassen, H.E., Energy from biomass: a review of combustion and gasification technologies. World Bank technical paper no. 422, Energy Series 1999.
Anderson, T., Doig, A., Rees, D. and Khennas, S., Rural Energy Services: A handbook for sustainable energy development. ITDG Publishing, 1999.
Tickell, J., Teickell, K., From the Fryer to the Fuel Tank: The Complete Guide to Using Vegetable Oil as an Alternative Fuel, Greenteach Publishing, 1999.
Pahl, Greg, Biodiesel: Growing a New Energy Economy. Chelsea Green Publishing, 2004 http://www.chelseagreen.com/2004/items/biodiesel.
This Howtopedia entry was derived from the Practical Action Technical Brief Biogas and Liquid Biofuels - Technical Brief.
To look at the original document follow this link: http://practicalaction.org/?id=energy
Useful addresses
Practical Action
The Schumacher Centre for Technology & Development, Bourton on Dunsmore, RUGBY, CV23 9QZ, United Kingdom.
Tel.: +44 (0) 1926 634400, Fax: +44 (0) 1926 634401
e-mail: practicalaction@practicalaction.org.uk
web: www.practicalaction.org
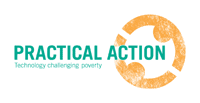
Categories
- Agriculture
- Urban Agriculture
- Biogas
- Cattle
- Farming
- Community
- Composting
- Construction
- Cooking
- Crops
- Energy
- Equipment Design
- Fertilizer
- Fruits
- Hygiene
- Ideas
- Recycling
- Resource Management
- Sanitation
- Small Business
- Vegetables
- Waste
- Irrigation
- Medium
- Global Technology
- Global
- Mediterranean Climate
- Monsoon Climate
- Rural Environment
- Tropical Climate
- Compost
- Concrete
- Cow dung
- Fuel
- Manure
- Oil
- Plastic container
- Sawdust
- Seeds
- Straw
- Termites
- Between 2 and 5 People
- More than 5 Persons
- Household
- Village
- Neighbourhood
- Application
- Principles